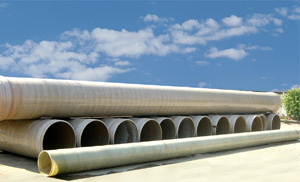
Recently from China's industrial anti-corrosion Technology Association, the marine industry second five! Plan, China's relevant departments will offshore structure corrosion control technology further deepen the development and expansion of new anti-corrosion technology and new composite materials will be become security guards marine engineering structures. FRP material as a lightweight, high strength corrosion-resistant materials, as early as anticorrosion decades ago into the ocean, such as glass fiber reinforced epoxy vinyl resin-based anti-corrosion lining, tank pipe, grille, splash zone FRP (fiberglass reinforced plastic namely FRP material) coating cathodic protection, pull wrapped FRP ribs, have already entered the port, offshore platforms and a range of marine anticorrosion. According to the requirements of the current state of marine construction and domestic marine FRP corrosion materials into the project as a whole is far from enough. Near the coast of the Pearl River Delta, Yangtze River Delta, Bohai Bay City Group fiberglass enterprises to actively seize the opportunity of the great development of marine anticorrosion efforts classic case inquiry and standards of the European and American markets, the initiative to strengthen the relevant scientific research institutes cooperation, and promote further the application of domestic anti-corrosion materials and fiberglass products.
In the glass steel material plays an important role in the
hollow glass microsphere exactly humble, and why it is so small things can bring such a big role. There are hollow glass microsphere resin system can be used to spray airless spray equipment, plus the glass fiber chopped strand mat cloth and other fabrics able to manufacture marine laminates. With different pressures within the system to select the appropriate type of hollow glass microspheres. More typical formulation is the volume content of the hollow glass microspheres was 22%, the corresponding content of about 5% by weight. Utilize lower shear mixing equipment so as to be able to be well dispersed in the resin.
Cenospheres having the smallest surface area and low oil absorption, it can be in a mixed species having good dispersibility, it is easy to be pressed and fused, so it has a high filling properties, can greatly reduce the amount of use of resin, the increase the amount of filler, effectively reducing the VOC indexes, while reducing costs.
Volume more cost performance cenospheres density is only a fraction of the resin density, only a small amount of cenospheres can replace heavier materials. When considering the cost per unit volume, rather than the cost per unit weight, high-performance hollow microspheres can significantly reduce costs.