Mar 19, 2020 (The Expresswire) — Global “Hollow Glass Microsphere Market” forecast report provides an in-depth analysis of all market dynamics including drivers and restraints, and trends and opportunities. The report covers the competitive scenario of the major market players here which specifies their sales revenue, customer demands, company profile, import/export scenario, business strategies that will help the developing market segments in creating major business conclusions. The report further highlights the primary challenges and latest growth approaches contained by key players that establish the dynamic competitive spectrum of this business domain.
Get a Sample Copy of the Report at -https://www.industryresearch.co/enquiry/request-sample/15333744
Impact of The Hollow Glass Microsphere Market Report:
A comprehensive evaluation of all opportunities and risks in the market.
Hollow Glass Microsphere market ongoing developments and significant occasions.
The detailed study of business techniques for the development of the market-driving players.
Conclusive study about the improvement plan of the market for approaching years.
Top to a bottom appreciation of market-express drivers, targets and major littler scale markets.
Favorable impressions inside imperative mechanical and publicize the latest examples prominent the market.
Inquire or Share Your Questions If Any Before the Purchasing This Report -https://www.industryresearch.co/enquiry/pre-order-enquiry/15333744
The report also focuses on global major leading industry players of the Global Hollow Glass Microsphere market providing information such as company profiles, product picture and specification, capacity, production, price, cost, revenue and contact information. Upstream raw materials and equipment and downstream demand analysis is also carried out.
On the basis on the end users/applications, this report focuses on the status and outlook for major applications/end users, sales volume, market share and growth rate of Hollow Glass Microsphere Market applications includes:
Aerospace
Automobile
Medical Care
Hollow Glass Microsphere Market Production by Regions:
United States
Europe
China
Japan
South Korea
Hollow Glass Microsphere Market report consumption with respect to other regions like Canada, Mexico, Asia-Pacific, China, India, Japan, South Korea, Australia, Indonesia, Malaysia, Philippines, Thailand, Vietnam, Europe, Germany, France, UK, Italy, Russia.
Purchase this Report (Price 2900 USD for a Single-User License) -https://www.industryresearch.co/purchase/15333744
The research provides answers to the following key questions:
What is the global (North America, South America, Europe, Africa, Middle East, Asia, China, Japan) production, production value, consumption, consumption value, import and export of Hollow Glass Microsphere?
Who are the global key manufacturers of Hollow Glass Microsphere industry? How is their operating situation (capacity, production, price, cost, gross and revenue)?
What are the types and applications of Hollow Glass Microsphere? What is the Hollow Glass Microsphere market share of each type and application?
What are the upstream raw materials and manufacturing equipment of Hollow Glass Microsphere? What is the manufacturing process of Hollow Glass Microsphere?
Economic impact on Hollow Glass Microsphere industry and development trend of Hollow Glass Microsphere industry.
What will the Hollow Glass Microsphere Market growth rate and size be in 2026?
What are the key factors driving the global Hollow Glass Microsphere industry?
What are the Hollow Glass Microsphere market trends impacting the growth of the Hollow Glass Microsphere Market?
What is the Hollow Glass Microsphere Market challenges to market growth?
What are the Hollow Glass Microsphere Market opportunities and threats faced by the vendors in the global Hollow Glass Microsphere Market?
from:marketwatch
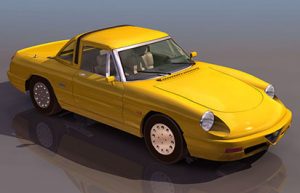
Sinosteel Maanshan New Material Technology Co., Ltd is a comprehensive high-tech enterprise, which specialized in research、development、production and sales of High-performance Hollow Glass Microspheres, and it belongs to Sinosteel Maanshan Institute of Mining Research Co.,Ltd.