In order to give full play to the effect of hollow glass microspheres, it is necessary to ensure that the hollow structure remains intact during the addition process. The strong shear in the twin-screw extruder can easily break the glass beads. Once the hollow glass beads are broken, they will become glass fragments with a density of 2.5g/cm3, which cannot achieve weight reduction. This is also the main reason why many application products did not achieve the desired effect in the initial stage of the experiment.
Therefore, how to reduce the breakage rate of microbeads in the twin-screw extruder granulation process is the key to the excellent performance of hollow glass microbeads.
Specifically, it can be considered from the extruder thread combination, feeding and pelletizing method, main engine speed, and compressive strength of microbeads.
01 . Adjustment of twin screw thread combination

In a twin-screw extruder, the shear force of the screw on the material makes the filler evenly dispersed. The spherical shape of the microbeads is easier to disperse, and excessive shear force can easily cause them to break. Therefore, the angle of the thread block of the meshing section should be adjusted, and the shear force should be reduced according to the low shear design. The specific adjustment method is as follows (real shot by St. Wright Laboratory):
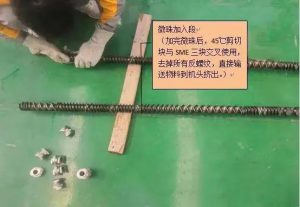
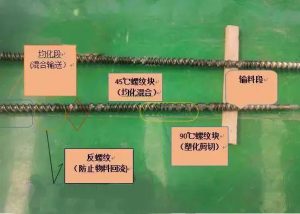
After improving the thread combination
Comparison of crushing rates caused by different feeding methods and granulation methods
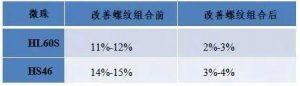
02. Adjustment of feeding method
To better reduce the bead breakage rate, you should:
1) Select side feeding to reduce the chance of microbeads being sheared in the screw.
2) Select long particles for granulation to reduce the damage of strong mechanical force during granulation.
After improving the thread combination
Comparison of crushing rates caused by different feeding methods and granulation methods
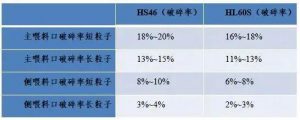
Remark:
1. Sanlight HS46, compressive strength: 16000psi, D90 (typical value) 30μm, specific gravity 0.46g/cm3.
2. Sanlight HL60S, compressive strength: 18000psi, D90 (typical value) 55μm, specific gravity 0.60g/cm3.
03. The influence of the rotational speed of the twin-screw machine
When the rotation speed is high, the shear force on the material is greater, which makes the microbeads more easily broken. Therefore, under the premise of ensuring the production process, reduce the speed and reduce the shear force of the screw.
After improving the thread combination, long particle granulation and side feeding conditions
Comparing the crushing rate caused by different screw speeds
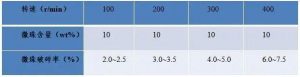
When the content of microbeads is about 10wt%, the crushing rate of microbeads increases with the increase of screw speed, and the crushing rate rises to 7.23% at 400r/min.
04. Common problems and solutions
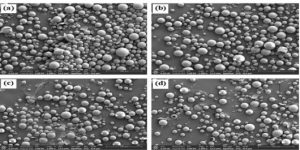
1) What is the normal breakage rate of microbeads during extrusion?
Due to the problem of the processing method, the microbeads will have a certain breakage rate during the extrusion process.
Optimization:
Adjust the screw combination, add microbeads to the side feed, granulate long particles, and the crushing rate can be controlled at 2-3%.
2) Does the addition of microbeads affect the resin processing performance?
Microbeads are an inorganic powder filler, similar to other inorganic fillers, which can improve the heat resistance of the resin after adding. Therefore, the processing temperature is increased.
solution:
1. The extruder is at the original processing temperature;
2. Add a small amount of lubricant to the formula to solve.
3) After the microbeads are fed from the side, how to ensure the uniformity of feeding?
solution:
1. Side feeding chooses twin-screw forced feeding;
2. A stirring rod should be added to the side feeding to prevent microbeads from “bridging” and ensure uniform feeding.
4) Will the mechanical properties of the resin drop significantly after adding microbeads?
Part of the impact performance will be sacrificed after adding microbeads, but part of the flexural modulus can be improved.
ways to improve:
1. Add a small amount of toughening agent;
2. Modify the surface of the microbeads with a coupling agent to improve the binding properties of the microbeads and the resin.
In addition, the compatibility of hollow glass microspheres with resin is not good, and the interfacial adhesion between resin and glass microsphere material will become poor, which will greatly reduce the performance of hollow glass microspheres, so improve the interfacial adhesion between them. Compatibility is very important.
Commonly used methods to improve compatibility include:
(1) Add compatibilizer: use coupling agent or maleic anhydride graft resin to improve the interface adhesion between the two;
(2) Surface etching: using acid and alkali to produce a large number of defects on the surface of the microbeads, at this time, the resin will be filled into the defect gap to achieve a stable effect;
(3) Surface modification: Through the reaction of strong oxidants and or acid-base and SiO, compatible functional groups such as silicon carboxyl groups and hydroxyl groups are generated; these functional groups can also be modified, and these modified functional groups can be grafted, polymerization and other reactions. Thereby improving the interfacial adhesion.
FROM: Eighth Element Plastic Edition